Revolutionizing Construction Sites: The Power of the Mobile Concrete Batching Plant
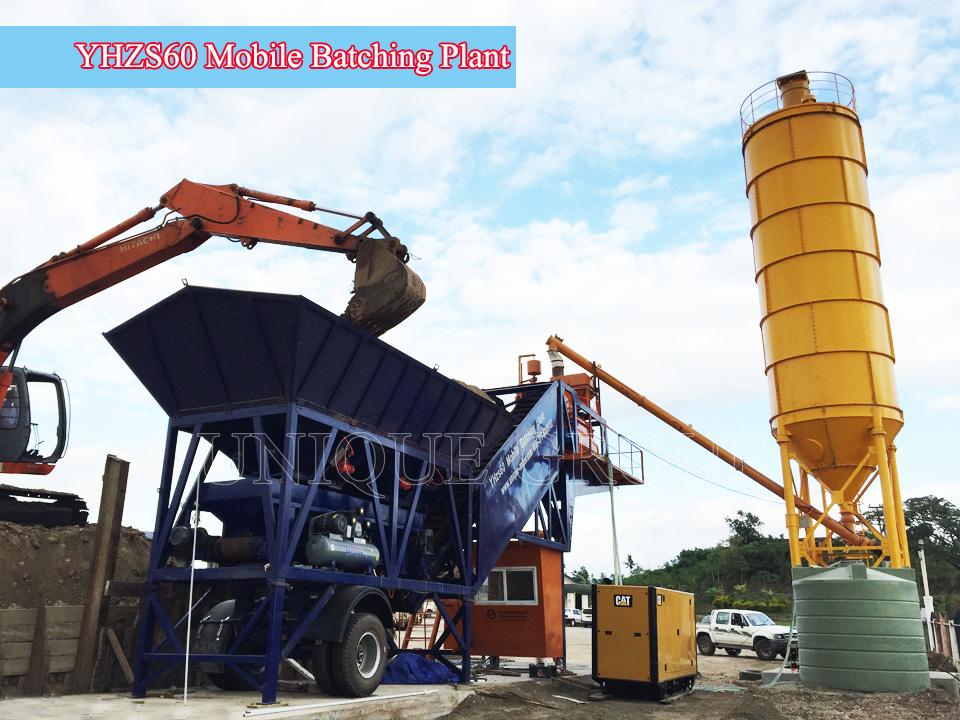
In the fast-paced world of construction, efficiency, flexibility, and timely delivery are paramount. Gone are the days when large-scale projects relied solely on distant stationary plants, enduring long waits and the risks associated with transporting ready-mix concrete over significant distances. Enter the mobile concrete batching plant – a game-changing innovation that brings the concrete production factory directly to the job site. As UNIQUEMAC, a leader in concrete equipment manufacturing, we understand the transformative impact this technology delivers. Let's delve into how these marvels of modern engineering work and why they are becoming indispensable for projects worldwide.
Understanding the Core Concept: On-Demand Concrete Production
At its essence, a mobile concrete batching plant is a fully integrated, self-contained production unit mounted on trailers or a single chassis. Unlike its stationary counterpart, it can be transported, set up, and commissioned relatively quickly – often within a matter of days. Its primary mission? To combine cement, aggregates (sand, gravel, crushed stone), water, and often admixtures in precise proportions to produce high-quality ready-mix concrete exactly where it's needed.
Deconstructing the Mobile Powerhouse: Key Components
While compact and mobile, these plants pack the full functionality of a traditional concrete batch plant. Let's break down the essential components of a concrete batch plant within the mobile configuration:
-
Aggregate Bins: These are multiple compartments (usually 2-4) mounted on the plant's frame, storing different sizes and types of aggregates (e.g., sand, coarse gravel, fine gravel). Feeders at the bottom regulate the flow.
-
Aggregate Conveyor Belt: A robust belt system transports the aggregates released from the bins towards the weighing and mixing area.
-
Cement Silo: A vertical storage tank, typically bolted for easy assembly/disassembly, holds the cement. It's equipped with dust filters and an air fluidization system to ensure smooth flow. Larger plants may have multiple silos.
-
Cement Screw Conveyor: This auger system accurately transfers cement from the silo to the weighing hopper.
-
Water Tank & System: Includes a water storage tank, pump, and piping to deliver the required amount of water. Often includes a meter for precise measurement. May include an admixture dosing system.
-
Weighing Hoppers/Scales: The heart of accuracy.
-
Aggregate Weigh Hopper: Positioned under the conveyor belt end, it receives and weighs each type of aggregate sequentially.
-
Cement Weigh Hopper: Receives cement from the screw conveyor and weighs it.
-
Water Scale: Measures the exact volume of water.
-
Admixture Scale (if applicable): Precisely doses liquid or powder admixtures.
-
-
Mixer: The core where the magic happens! The weighed ingredients are discharged into the mixer. Common types include:
-
Twin Shaft Mixer: Highly efficient, fast mixing, excellent for harsh mixes and high production rates. Common in larger mobile plants.
-
Pan Mixer: Effective for various mix designs, good homogenization.
-
Drum Mixer (Less common in mobile plants): Similar to a transit mixer drum, often used in very compact units.
-
-
Control System: The "brain" of the operation. A sophisticated control system, housed in an operator cabin, manages the entire batching process. Operators input mix designs, and the system automates the sequencing of feeders, conveyors, weighing, charging, mixing times, and discharging. Modern systems feature touchscreen interfaces, recipe storage, production reporting, and diagnostics.
-
Chassis/Frame: The robust mobile platform (often with axles and kingpin for towing) that integrates all components. Designed for stability during operation and transportability. Hydraulic legs provide support and leveling on-site.
-
Discharge System: The mixed concrete is typically discharged directly into waiting dump trucks, concrete pumps, or wheelbarrows. Some plants have a short discharge conveyor.
The Working Symphony: How a Mobile Concrete Batching Plant Operates
The process is a marvel of coordinated automation:
-
Setup & Calibration: The plant is transported to the site, leveled, and stabilized. Aggregate bins are loaded, the cement silo is filled (often via pneumatic tanker), and the water tank is filled. The control system is powered up, mix designs are loaded, and scales are calibrated.
-
Initiating a Batch: The operator selects the desired concrete mix recipe and batch size on the control system panel and initiates the cycle.
-
Aggregate Batching: The control system signals the first aggregate bin feeder to open, releasing material onto the aggregate conveyor belt. The belt carries it to the aggregate weigh hopper. Once the target weight for that aggregate is reached (monitored by the scale), the feeder closes. The process repeats sequentially for each required aggregate type directly into the same weigh hopper.
-
Cement Batching: Simultaneously or sequentially, the control system activates the cement screw conveyor, feeding cement from the cement silo into the cement weigh hopper until the precise weight is achieved.
-
Water & Admixture Batching: The water system pumps the exact amount of water into the water weigh tank. Any required admixtures are dosed into their dedicated scale or directly into the water line.
-
Charging the Mixer: Once all materials are weighed, the control system commands the discharge gates of the aggregate weigh hopper, cement weigh hopper, and the water/admixture system to open. The materials fall (or are sometimes conveyed) into the waiting mixer.
-
Mixing: The mixer starts (either before or immediately after charging begins) and runs for a predetermined time set in the recipe – typically 30-90 seconds – ensuring a completely homogeneous ready-mix concrete.
-
Discharging: Upon completion of mixing, the mixer discharge door opens, and the fresh concrete is released into the transport vehicle or placement equipment below.
-
Cycle Repeat: The plant is ready to start the next batch immediately. The control system logs the batch data.
Why Choose Mobile batching plant? The Compelling Advantages
The mobile concrete batching plant offers distinct benefits that directly translate to project success:
-
Unmatched Flexibility & Mobility: Deploy rapidly to remote sites, urban locations, or projects with multiple phases spread over a large area. Relocate easily as the project progresses.
-
Significant Cost Savings: Eliminates or drastically reduces the high costs and environmental impact associated with long-distance ready-mix concrete trucking. Minimizes concrete waste due to setting during transit.
-
Freshness & Quality Control: Produces concrete directly at the point of placement, ensuring maximum freshness, workability, and strength development. Allows for immediate adjustments to mix designs based on site conditions.
-
On-Demand Production: Produce concrete exactly when needed, reducing wait times for trucks and preventing delays. Ideal for projects with tight schedules or continuous pours.
-
Reduced Site Footprint: Modern mobile plants are designed to be compact, requiring less space than establishing a temporary stationary plant setup.
-
Faster Project Timelines: By eliminating transport delays and enabling immediate concrete availability, projects can progress significantly faster.
-
Versatility: Capable of producing a wide range of concrete mixes, from standard grades to specialized formulations.
UNIQUEMAC: Your Partner in Mobile Concrete Solutions
As a professional concrete equipment manufacturer, UNIQUEMAC is dedicated to providing cutting-edge, reliable, and efficient mobile concrete batching plants. We understand the critical demands of modern construction. Our plants are engineered with robust components of a concrete batch plant, featuring advanced control systems for precision batching, high-performance mixers for consistent quality, and rugged designs built for the challenges of site deployment and transport.
Whether you're a contractor tackling large infrastructure projects, a developer building in a constrained urban environment, or involved in disaster recovery efforts, a UNIQUEMAC mobile concrete batching plant empowers you with control, efficiency, and the ability to deliver high-quality ready-mix concrete precisely where and when it's needed.
Embrace the Future of On-Site Production
The mobile concrete batching plant is more than just equipment; it's a strategic advantage. It represents a shift towards smarter, more responsive, and cost-effective construction methodologies. By bringing the batching plant to the project, you gain unprecedented control over your concrete supply chain, ensuring quality, saving time and money, and ultimately driving project success. Explore UNIQUEMAC's range of mobile solutions today and experience the transformation in your concrete operations.
- Information Technology
- Office Equipment and Supplies
- Cars and Trucks
- Persons
- Books and Authors
- Tutorials
- Art
- Causes
- Crafts
- Dance
- Drinks
- Film
- Fitness
- Food
- Игры
- Gardening
- Health
- Главная
- Literature
- Music
- Networking
- Другое
- Party
- Religion
- Shopping
- Sports
- Theater
- Wellness
