-
- EXPLORAR
-
-
-
-
-
-
-
-
Maximizing Efficiency: The Working Process of Aggregate Crusher Plants Explained
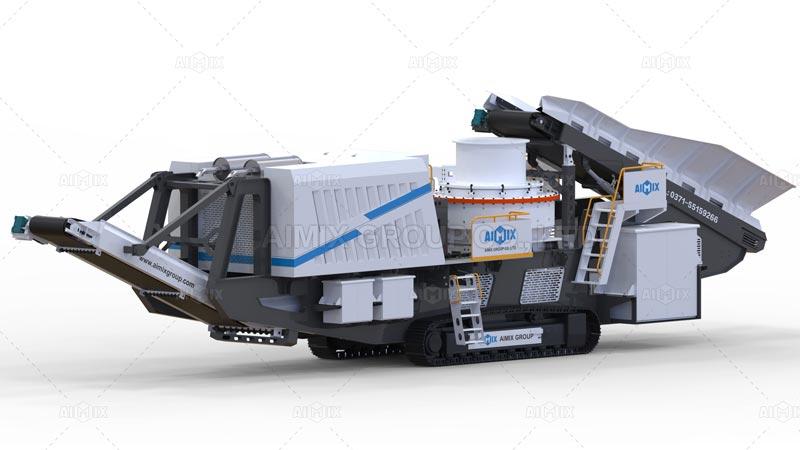
Aggregate crusher plants play a crucial role in the construction and mining industries by providing the essential materials needed for various projects. From road construction to building infrastructure, these facilities are designed to crush and process a variety of rocks and aggregates into usable products. Understanding the working processes of aggregate crusher plants, including both stationary and mobile stone crusher plants, can help businesses maximize their efficiency and productivity. In this article, we will delve into the operational processes, key components, and maintenance practices that ensure optimal performance.
Understanding Aggregate Crusher Plants
Aggregate crusher plants are designed to produce various sizes of aggregates for construction purposes. The production process involves several stages, including feeding, crushing, screening, and stockpiling. Each stage is critical to achieving the desired quality and size of the final product.
Types of Aggregate Crusher Plants
-
Stationary Aggregate Crusher Plants:
Stationary plants are fixed installations that are usually set up in one location for large-scale operations. These aggregate plants(AIMIX plantas de agregados) are designed for high production volumes and offer efficient processing of raw materials. They are ideal for ongoing projects requiring a consistent supply of aggregates. -
Mobile Stone Crusher Plants:
Mobile plants, on the other hand, are portable and can be moved from one job site to another. This flexibility makes them suitable for smaller operations or projects that require frequent relocation. Mobile stone crusher plants can adapt to different site conditions and production needs.
The Working Process of Aggregate Crusher Plants
The efficiency of an aggregate crusher plant relies heavily on its operational processes. Here, we will break down the key stages involved in the production of aggregates.
1. Feeding the Material
The process begins with the feeding of raw materials into the plant. This is typically done through hoppers or conveyors, which transport the material to the primary crusher. The feeding system is crucial, as it ensures a steady and controlled flow of material, minimizing bottlenecks and maximizing efficiency.
2. Crushing the Aggregates
Once the materials are fed into the mobile plant(trituradora de piedra móvil), they undergo the crushing process. Different types of crushers are used based on the desired output and material characteristics:
-
Jaw Crushers: These crushers are commonly used for primary crushing, effectively breaking down large rocks into smaller sizes. They operate using a fixed and a movable jaw, creating a compressive force to crush the material.
-
Cone Crushers: Ideal for secondary and tertiary crushing, cone crushers provide a finer product size. They work by using a rotating mantle that crushes the material against a stationary concave.
-
Impact Crushers: These crushers utilize high-speed impact forces to break down the material. They are particularly effective for softer materials and produce high-quality aggregates.
3. Screening the Material
After crushing, the material is screened to separate different sizes of aggregates. Screening ensures that only the desired sizes are processed further, while larger particles are sent back for additional crushing. This stage often involves multiple screens that sort the material based on size, allowing for efficient production of various aggregate grades.
4. Stockpiling
Once the aggregates are sized correctly, they are stockpiled for storage or shipment. Proper stockpiling techniques help maintain the quality of the aggregates and make them easily accessible for transport. Efficient stockpiling also prevents contamination and degradation of the materials.
Maintaining Aggregate Crusher Plants
To maximize efficiency, regular maintenance is essential for aggregate crusher plants. Proper upkeep of equipment ensures reliable operation and prevents costly downtime. Here are some key maintenance practices:
1. Regular Inspections
Conducting routine inspections of the crushers, screens, and conveyors can help identify potential issues before they escalate. Checking for wear and tear, loose components, and lubrication levels is crucial for maintaining optimal performance.
2. Equipment Calibration
Ensuring that all equipment is calibrated correctly allows for consistent production and quality control. Regularly calibrating crushers and screens can help maintain the desired output sizes and improve overall efficiency.
3. Staff Training
Investing in staff training is vital for ensuring that operators understand how to run the equipment efficiently and safely. Well-trained personnel can identify problems quickly and take corrective actions to minimize downtime.
4. Implementing Preventative Maintenance
Establishing a preventative maintenance schedule can help reduce the likelihood of unexpected breakdowns. Regularly replacing worn-out parts, cleaning the equipment, and performing necessary repairs can extend the lifespan of the plant and improve its productivity.
Conclusion
Aggregate crusher plants are essential components of the construction and mining industries, providing the necessary materials for various projects. By understanding the working processes of both stationary and mobile stone crusher plants, businesses can maximize their efficiency and productivity. Implementing proper maintenance practices and ensuring that staff are well-trained will further enhance operational performance. With the right knowledge and practices, companies can optimize their aggregate production and contribute to the success of their projects.
- Information Technology
- Office Equipment and Supplies
- Cars and Trucks
- Persons
- Books and Authors
- Tutorials
- Art
- Causes
- Crafts
- Dance
- Drinks
- Film
- Fitness
- Food
- Jogos
- Gardening
- Health
- Início
- Literature
- Music
- Networking
- Outro
- Party
- Religion
- Shopping
- Sports
- Theater
- Wellness
