Copper Cyanide Manufacturing Plant Project Report 2025: Market Trends, Process, and Project Insights
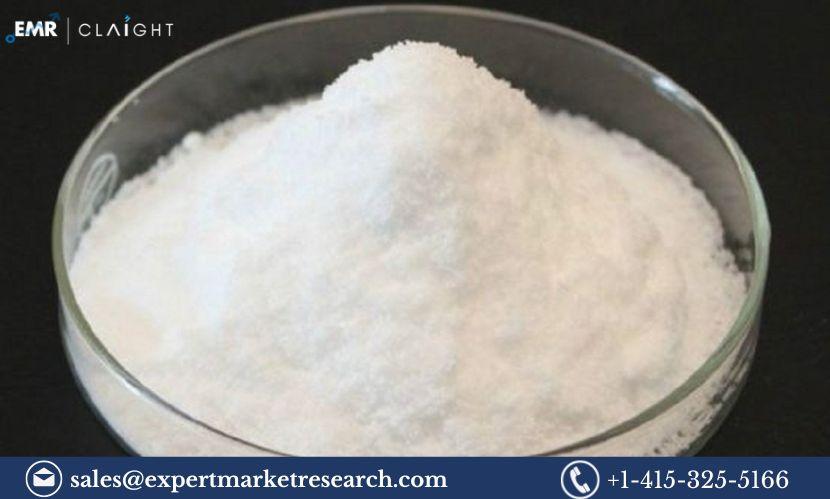
Introduction
The Copper Cyanide Manufacturing Plant Project Report serves as a comprehensive guide to setting up a plant focused on the production of copper cyanide, a compound that plays a crucial role in various industrial processes, particularly in gold mining and electroplating. Copper cyanide is used primarily in the extraction of gold and in electroplating operations where it helps in forming thin copper coatings on metal surfaces. The success of a copper cyanide manufacturing plant requires careful planning, from understanding market demands to assessing environmental concerns and regulatory compliance. This project report offers insights into the setup, operational considerations, and financials associated with establishing a copper cyanide production facility.
In this article, we explore the various aspects of starting a copper cyanide manufacturing plant, including its significance in industrial applications, production processes, key equipment, market potential, regulatory requirements, and potential challenges.
Importance of Copper Cyanide
Copper cyanide is a compound with several important industrial uses. One of its primary applications is in gold extraction, where it forms the basis of the cyanidation process. This chemical compound is used to dissolve gold from ore, allowing for efficient gold extraction. Additionally, copper cyanide plays a significant role in electroplating, where it is used as a plating solution for coating various metals with copper.
The versatility of copper cyanide in different sectors, coupled with the increasing demand for gold and metal plating, makes it a valuable product in the global market. The growing industries of electronics, automotive, and jewelry manufacturing also contribute to the sustained demand for copper cyanide.
Market Demand and Scope of Copper Cyanide Production
Before embarking on a copper cyanide manufacturing plant project, it is crucial to understand the market dynamics. The demand for copper cyanide is primarily driven by the mining industry, especially gold mining operations. As gold prices fluctuate and mining activities increase globally, the need for copper cyanide in the extraction process continues to rise.
Additionally, copper cyanide is in demand within the electroplating industry, which is constantly growing due to the rising need for copper-coated products in the manufacturing of electrical components, connectors, and other industrial equipment. The electronics sector, in particular, is a major consumer of electroplated copper components, further driving the demand for copper cyanide.
The geographic location of the plant is another important factor to consider. Areas with a high concentration of gold mines or regions with significant manufacturing capabilities for electroplated goods present potential markets for copper cyanide. Understanding the scope of local demand and the proximity to these industries can help a manufacturing plant establish its position in the market and optimize its operations.
Get a Free Sample Report with Table of Contents@
Production Process of Copper Cyanide
The production of copper cyanide involves several critical steps that ensure the product's quality and consistency. Although there are different methods for manufacturing copper cyanide, the most common process involves the following stages:
-
Raw Material Procurement: The first step in the manufacturing process is the acquisition of raw materials such as copper salts, sodium cyanide, and water. These are the fundamental ingredients used to synthesize copper cyanide.
-
Reaction Process: The copper salts and sodium cyanide are reacted together in a controlled environment. The chemical reaction produces copper cyanide and other by-products. To maintain high-quality output, it is essential to control factors such as temperature, pressure, and the ratio of ingredients.
-
Purification and Filtration: After the reaction, the solution contains copper cyanide, along with impurities. These impurities must be removed through filtration and purification processes. This ensures that the final product meets the required purity standards for industrial applications.
-
Crystallization: The purified copper cyanide is then crystallized to separate it from the remaining solution. The crystallization process results in the formation of solid copper cyanide crystals, which are then dried to obtain the final product.
-
Packaging and Distribution: Once the copper cyanide is dried and prepared for sale, it is packaged and distributed to customers. It is important to package copper cyanide in safe, secure containers to prevent accidents and ensure its safe handling during transport.
Throughout the production process, stringent quality control measures must be implemented to ensure the copper cyanide meets the necessary specifications. Regular testing and monitoring of key parameters, such as purity levels, will help maintain product consistency and reliability.
Key Equipment and Infrastructure
Setting up a copper cyanide manufacturing plant requires specific machinery and infrastructure to handle the raw materials, facilitate the chemical reaction, and ensure safe operations. Some of the key equipment needed for a copper cyanide production facility include:
-
Reactors: These are essential for the chemical reaction between copper salts and sodium cyanide. Reactors should be equipped with temperature and pressure control systems to maintain the desired reaction conditions.
-
Filtration Systems: Filtration units are used to remove impurities and contaminants from the copper cyanide solution after the reaction process. This helps ensure the final product is free from unwanted substances.
-
Crystallizers: Crystallizers are used to separate solid copper cyanide from the remaining solution. The crystallization process is vital for obtaining pure copper cyanide crystals.
-
Drying Equipment: After crystallization, the copper cyanide is dried to remove any moisture. This can be achieved using rotary dryers or other drying systems designed for chemical products.
-
Packaging and Storage Units: Packaging units are used to securely pack copper cyanide in containers that are safe for transportation and storage. Storage facilities should be well-ventilated and designed to safely store chemical products.
-
Safety Equipment: Given the toxic nature of cyanide compounds, safety equipment such as gas detection systems, protective clothing, and emergency response kits are necessary to protect workers and the surrounding environment.
Regulatory and Safety Considerations
The manufacturing of copper cyanide comes with stringent safety and environmental regulations due to the hazardous nature of cyanide compounds. Compliance with national and international safety standards is essential to prevent accidents and ensure safe operations. The regulatory framework often requires the following:
-
Environmental Impact Assessments (EIA): Before the plant is set up, an EIA should be conducted to evaluate the potential environmental effects of copper cyanide production. This includes assessing the risk of water contamination, air pollution, and chemical waste disposal.
-
Health and Safety Standards: The plant must adhere to worker safety protocols, including the proper handling of toxic chemicals and the provision of personal protective equipment (PPE). Regular safety training and emergency response drills are necessary to mitigate potential hazards.
-
Waste Management: Proper disposal of chemical waste and by-products is critical to prevent environmental pollution. The plant must establish waste management systems that safely handle hazardous materials, including spent cyanide solutions and contaminated residues.
-
Certification and Licensing: The copper cyanide manufacturing plant must obtain the necessary permits and certifications from relevant regulatory authorities. This may include health, safety, and environmental certifications, as well as compliance with industrial standards such as ISO.
Challenges
While the copper cyanide manufacturing industry offers lucrative opportunities, there are several challenges that plant operators may face:
-
Environmental Concerns: The use of cyanide in manufacturing processes raises environmental concerns. It is essential to implement effective waste management systems and adopt sustainable practices to minimize environmental impact.
-
Raw Material Sourcing: Securing a consistent and reliable supply of raw materials, particularly sodium cyanide and copper salts, can be challenging due to fluctuating prices and supply chain disruptions.
-
Technological Advancements: The chemical industry is constantly evolving, and technological advancements may impact production processes. Staying up-to-date with new technologies and production methods is crucial to maintaining competitiveness.
-
Market Volatility: The prices of copper and gold, which are linked to copper cyanide production, can fluctuate significantly. This can impact the profitability of the plant, especially when operating in markets with unpredictable demand.
FAQ
1. What is the primary use of copper cyanide?
Copper cyanide is mainly used in gold mining for the extraction of gold from ores and in electroplating processes to coat metals with a thin layer of copper.
2. What safety measures should be taken during the manufacturing process?
Safety measures include providing personal protective equipment (PPE) for workers, installing gas detection systems, ensuring proper ventilation, and following standard safety protocols for handling hazardous chemicals.
3. How can a copper cyanide manufacturing plant reduce environmental impact?
A plant can reduce environmental impact by implementing waste treatment systems, recycling waste products, and adhering to environmental regulations for disposal and emissions.
4. What are the key challenges in establishing a copper cyanide manufacturing plant?
Key challenges include securing a reliable raw material supply, managing environmental risks, adhering to safety standards, and coping with market volatility.
5. How does the global demand for copper cyanide affect the industry?
The global demand for copper cyanide is driven by the gold mining and electroplating industries. Fluctuating demand for these industries can influence copper cyanide production, pricing, and market trends.
Media Contact
Company Name: Claight Corporation
Contact Person: Lewis Fernandas, Corporate Sales Specialist — U.S.A.
Email: sales@expertmarketresearch.com
Toll Free Number: +1–415–325–5166 | +44–702–402–5790
Address: 30 North Gould Street, Sheridan, WY 82801, USA
Website: www.expertmarketresearch.com
Aus Site: https://www.expertmarketresearch.com.au
- Information Technology
- Office Equipment and Supplies
- Cars and Trucks
- Persons
- Books and Authors
- Tutorials
- Art
- Causes
- Crafts
- Dance
- Drinks
- Film
- Fitness
- Food
- Games
- Gardening
- Health
- Home
- Literature
- Music
- Networking
- Other
- Party
- Religion
- Shopping
- Sports
- Theater
- Wellness